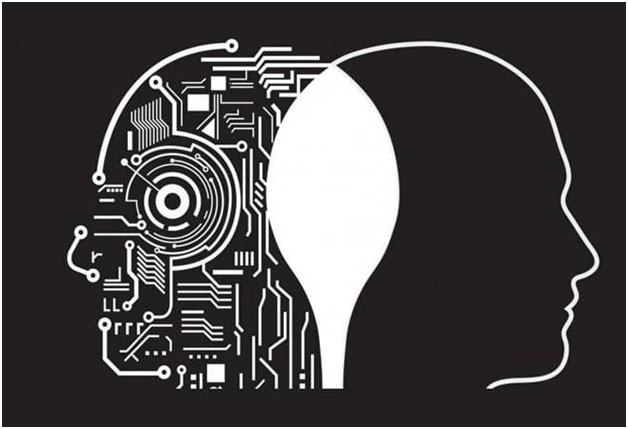
It’s the new norm in Industry 4.0 made possible by the revolutionary practice of digital twinning.
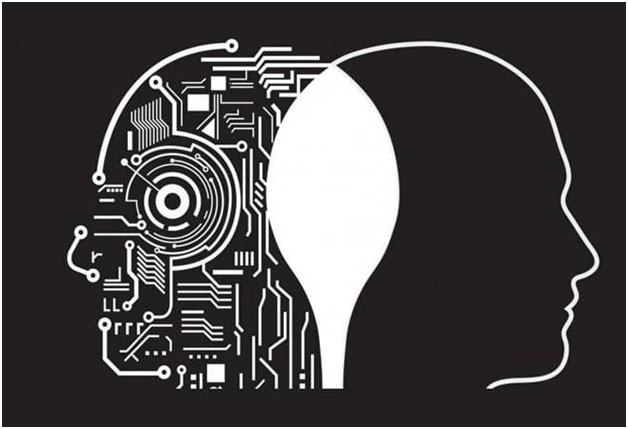
With time to market for a new product or process spiralling down to half, the cost of development reducing to a mere fraction, production systems getting 30% speedier and 25% more efficient, and downtimes almost tending towards zero, it may seem like any manufacturer’s dream come true. Only, it isn’t wishful thinking. It’s the new norm in Industry 4.0 made possible by the revolutionary practice of digital twinning.
India gearing up for change and the digital relevance
For India, the next decade of manufacturing will focus on adopting cognitive solutions that infuse intelligence into all processes- from a factory’s floor to the finished product. The thrust is upon the manufacturing sector to grow its contribution from 15% to 25% of the country’s GDP. SMEs in India, which have a share of 40% in the industrial production and employ close to 36 million people, can play a defining role in Industry 4.0.
One can maximize the potential with Digitalisation to enhance efficiency to fight scale, reduce the cost of production, minimise manufacturing defects, and shorten production time. Leveraging the full might of cutting-edge digital technologies, digital twins virtually mimic plant and factory products and processes.
In the product development cycle, manufacturers can virtually design, develop and test products with a high degree of precision, satisfying all parameters that matter. It’s like a dry run without incurring the prohibitive costs of developing physical prototypes.
Let us set the context by defining the concept of digital twin. For starters, Digital twin means an integrated multi-physics, multi-system simulation of a complex product, which functions to mirror the life of its corresponding twin. Digital twin consists of three parts- (i) the virtually defined product including its subsystems (ii) the physical product and (iii) the links between physical and virtual product. It serves as a bridge between the physical world and the digital world.
The digital twin is characterised by the two-way interactions between the digital and physical worlds, which may result in many benefits. In the physical world, the real product can be made smarter to actively adjust its real-time behaviour according to the recommendations made by the virtual product or the twin. Whereas in the virtual world, the digital version of the product can be made more realistic to accurately reflect the real-world state of the physical product.
In process-driven functions, digital twins constantly receive data feeds from interconnected machines, helping in predictive maintenance and running the business as usual without downtime. Gartner estimates that by 2021 – just a couple of years from now — half of all major industrial companies will be using digital twins. Key Industry verticals will be a key beneficiary of this.
With a new model being launched on an average every six months or so, a digital twin of the model serves as a test bed, helping manufacturers to design, customise and test every part while running it in a virtual environment, saving crucial time and millions on developing physical prototypes. Engineers can simulate and validate product properties, for example – Is the product stable, and is it intuitive to use? Does the car bodywork offer the lowest possible air resistance? Do the electronics operate reliably?
For Ford Motors, Siemens’ Digital Enterprise Suite operates across its value chain. It enabled Ford to increase their number of models, reduce factory energy cost by up to 30% and development time by up to 40%.
The same advantages are seen even in the heavy machinery industry. Let’s say, for example, a manufacturer needs to develop a steam turbine. Traditionally, engineers would take several months to design the product, physically build it and then test it for performance. On the other hand, by using a digital twin, they can test and evaluate all parameters with high precision — ranging from material to performance, while obtaining valuable data that would help make the final set of changes before the actual turbine is developed.
NASA’s Mars Science Laboratory mission – which includes the latest rover, popularly known as Curiosity – is the most technologically complex project in the space agency’s history. It is an example of the seamless communication that is developing among machines – the meeting of the real and virtual worlds.
In process industries, digitalisation enables companies to build a comprehensive data model, ensuring shorter time to market, greater flexibility, and increased efficiency, while allowing companies to respond successfully to the volatility and diversity of global markets, thereby giving them a lasting competitive edge.
The backdrop to the digital twin practice is digitalisation, which offers immense possibilities in redefining the ‘productivity’ criteria as businesses get access to high-quality data through digital real-time supply chain, digital product definition and digitally crafted and run production lines. By familiarising themselves with the application of digital twins, both SMEs and large organisations can integrate their engineering and operations functions and realise these time and cost efficiencies.
Industries and verticals looking to the future with digital twins
Today digital twins serve a wide range of industry sectors including automotive, food and beverages, pharmaceuticals, power utilities, transportation & logistics, aerospace & defence, and data centres, to name a few.
For example, the shop floor of a pharmaceutical company works with high-end machines that need the highest level of precision and functionality for optimal performance. There is almost no room for error here. A digital factory representing this entire process of drug manufacturing would provide a plethora of vital information about the current performance levels of these machines, and help predict errors and failures in advance, thereby saving the huge cost of having to deal with a fault unprepared.
This saves time and lays the groundwork for customised mass production, since even highly complex production routes can be calculated, tested, and programmed with minimal cost and effort in a short span of time, helping manufacturers meet their customers’ requirements.
Harnessing the power of digital twin technology, SMEs in India can ramp up, upgrade and adopt new designs and components much faster to stay aligned with the needs of OEMs. To realise this value, India will need to build an ecosystem of tier 1, tier 2, and tier 3 suppliers that bring a high level of efficiency, flexibility and quality focus to the table.
While IDC’s earlier prediction seems to have come true that by 2018, companies who invest in digital twin technology will see a 30% improvement in cycle times of critical processes, it primarily is the adoption rate of this technology that will determine if this can have a cascading effect on industries and the economy in general. With the benefits of adoption far outweighing the risks and consequences of living without it, it is only a matter of time before its use is implemented across functions and verticals in businesses.